Automated CAD Model Analysis
Blog Post 1.01.02 - Automated CAD Model Analysis to Drive Design for Manufacturing
Reduce and eliminate shop floor rework by testing your parts before they leave engineering. Read More ...
Global Edge Video Blog-1.01
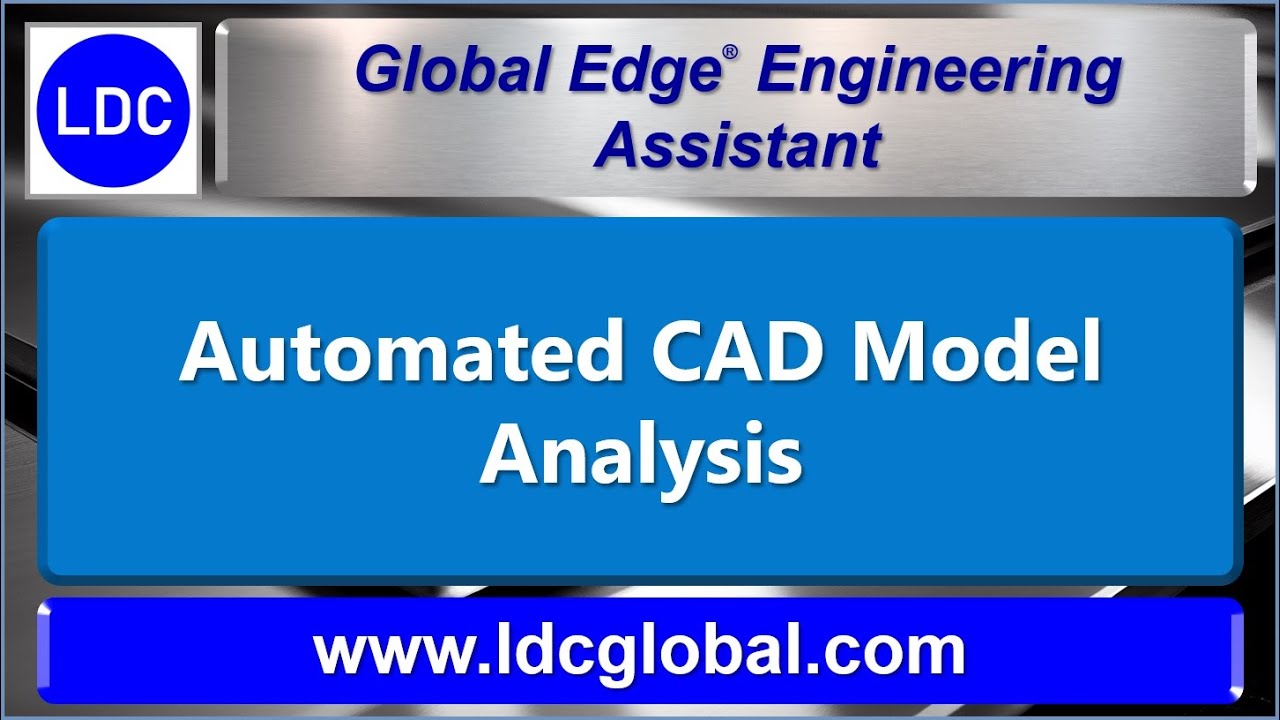
Video can’t be displayed
This video is not available.
Automated CAD Model Analysis to Drive Design for Manufacturing
A key element when it comes to collaboration between engineering and manufacturing is to establish processes that meld the design engineering process with manufacturing capabilities. This process is significantly strengthened when applying “Design for Manufacturing” software capabilities. The Global Edge Engineering Assistant includes powerful and innovative software functions to achieve effective Design for Manufacturing capabilities.
To achieve Design for Manufacturing capabilities, the Global Edge Engineering Assistant starts with “Automated CAD Part Analysis” that performs a complete analysis of a 3D CAD sheet metal part and stores the following CAD part parameters:
To achieve Design for Manufacturing capabilities, the Global Edge Engineering Assistant starts with “Automated CAD Part Analysis” that performs a complete analysis of a 3D CAD sheet metal part and stores the following CAD part parameters:
- Pem Holes Too Close to Bend Line
- Maximum Bend Tonnage Greater Than Bend Process Allows
- Part Too Big for Bend Process
- Bend Angle Exceeds Maximum Allowed
- Embossment Too Close to Bend Line
- Bend Line Length Shorter than Minimum Allowed
These CAD part parameters are subsequently stored in the Global Edge database to serve as a foundation for a “Manufacturability Testing” process. The CAD part parameters include identification up and down bends counts, location of Pem Hole and Louver distance from a bend line, including cutout counts and cutout perimeters, etc.
The next step in the Manufacturability Testing process is to automatically compare your CAD part parameters with your matching user definable Bend Processes as illustrated with the following Sample Bend Process:
The final step in the Manufacturability Testing process is an engineer selecting either a single part, or a large batch of sheet metal parts:
Then after selecting a single part, or batch of parts sheet metal parts to perform Manufacturability Testing on, the engineer can then select a sheet metal part to view the results of the test:
The above and below example includes 22 tests that were performed on the selected part. The highlighted test below (Minimum Down Pem Gap) detected a warning that “Feature Within Warning Gap”. The matching Bend Process for the sheet metal part requires the Minimum Down Pem Gap is at least 1.500000 inches from the nearest bend line. The detected gap with the selected sheet metal part is 1.800000 inches, which indicates the gap is allowable. However, a Warning Message is detected because ideally with the matching Bend Process indicates that the Minimum Down Pem Gap should ideally be at least 2.000000 inches.
Eliminate Shop Floor Mistakes
To see a demonstration as to how the Global Edge Engineeering Assistant can save your company significant time, money and eliminate shop floor mistakes, click on the link below to schedule a software demonstration.